
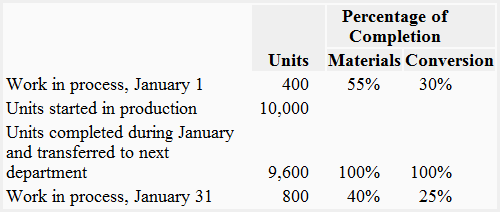
It will be very tough for the company for the low selling product, as the cost will low too. Price led costing: the cost of production will change depending on the selling price, as we can see in the formula.These are the principle of target costing: Target costing is a modern costing concept which needs to work backward from the selling price to total cost. Hence, he expects that this cost will decrease in next month. Type of Cost Target Actual Variance Direct Materials 3 3 0 Direct Labors 4.5 5 0.5 Overhead Cost 1 1 0 Total Cost 8.5 9 0.5Īfter investigation, the production manager found that the reason for the labor cost gap is due to the workers are still in the learning curve. In conclusion, ABC decides to produce this tumbler.Įvery month, ABC needs to compare the actual cost and target cost any variance needs to investigate and find a solution. Moreover, the purchasing department will be able to get a bulk discount from suppliers when they buy more than 10,000 units. As a result, ABC will be able to save $1 per unit from direct labor due to the learning curve after one month. The production manager has conducted a meeting with relevant departments to find a way to reduce all variable costs to $8.5. The production manager has calculated the variable cost as below: It is not willing to increase its selling price because it is hard to differentiate from other products in the market.īase on ABC’s policy, the profit margin should not be less than 15% of the selling price.
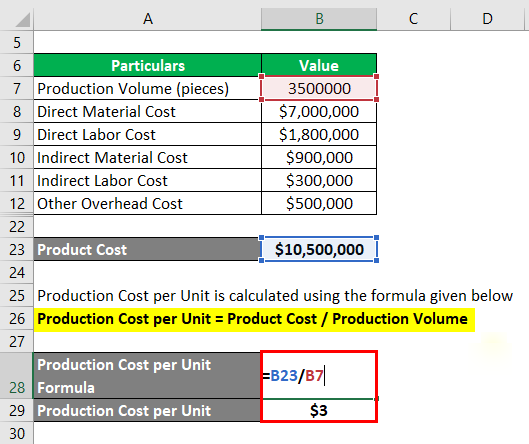
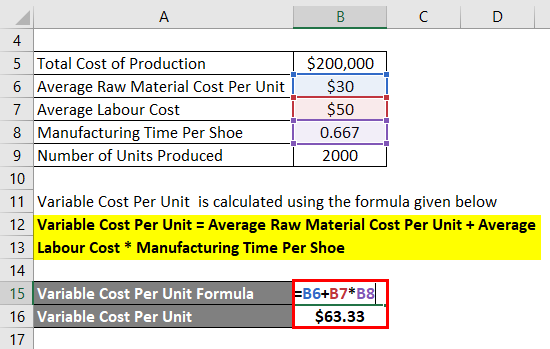
After conducting market research, the average price is $10 per unit. Target Costing ExampleĬompany ABC produces tumbler for a very competitive market, due to the similarity with many other suppliers. In this case, we need to keep monitoring this process over time. The gap usually results from an inefficient process that requires improvement. – Take action to close the cost gap: We need to analyze the production cost from the beginning to the end to find the root causes. So, during production, we need to compare the exact cost and target cost. – Calculate cost gap: Cost gap occurs when the actual cost is higher than the target cost. – Calculate target cost: Calculate target cost by deducting the target profit from selling price, which set in the previous step. – Set target profit: We need to follow our company target profit that decided by top management. It can be a benchmark from the market and competitors. – Set selling price : We need to set a specific selling price which aligns with the market and customers. In order to determine the target costing, we need to follow below processes: Additionally, we should try to find out which products feature customer need so that we can fill the gap in the market. We need to look at competitors’ selling price as well as customers’ behavior of how much they are willing to pay. If the actual cost is higher than target cost, it will require our investigation in order to find the solutions to close the gap. If the result is the other way round, we are good to go no action required.Ĭonduct market research: We need to conduct market research on the product we intend to produce. After that we regularly compare the target cost with the actual production cost. We usually design the target costing at the planning stage of productions. Target Cost = Selling Price / (1 + Profit %) Target Cost = Selling price – (Selling price x Profit %) If the profit margin base on the selling price: To calculate the target costing, we simply use the following formula: To maintain the target profit margin, the company needs to reduce total cost. The company set the target cost, which includes all the costs, at the minimum level. A small change in price will have a massive impact on sale volume.

We use this strategy in a competitive market because it is hard to increase the selling price due to its elasticity. The desirable profit is the expected return from the shareholder. The target costs include variable cost, fixed cost, and manufacturing overhead costs. In order to use this method, total costs must be equal or less the target cost otherwise it will impact profit margin or selling price. It is the maximum cost which the company can go for otherwise they should not produce the product. Target Cost is the remaining balance after deducting profit from selling price. Company uses this strategy by setting the selling price, determine desirable profit, and calculate the target cost. Target costing is the method which company sets the production cost by deducting profit margin from the target selling price.
